Unlocking New Assembly Technologies to Drive Intelligence and Safety in Car Door Locks
Car door locks, as an important part of the vehicle body, are installed on the car doors and their pillars, responsible for reliably locking the doors and playing a crucial role in the overall safety of the vehicle. If the door locks become loose, it not only affects the normal use of the vehicle but also poses a potential risk to the vehicle's overall safety.
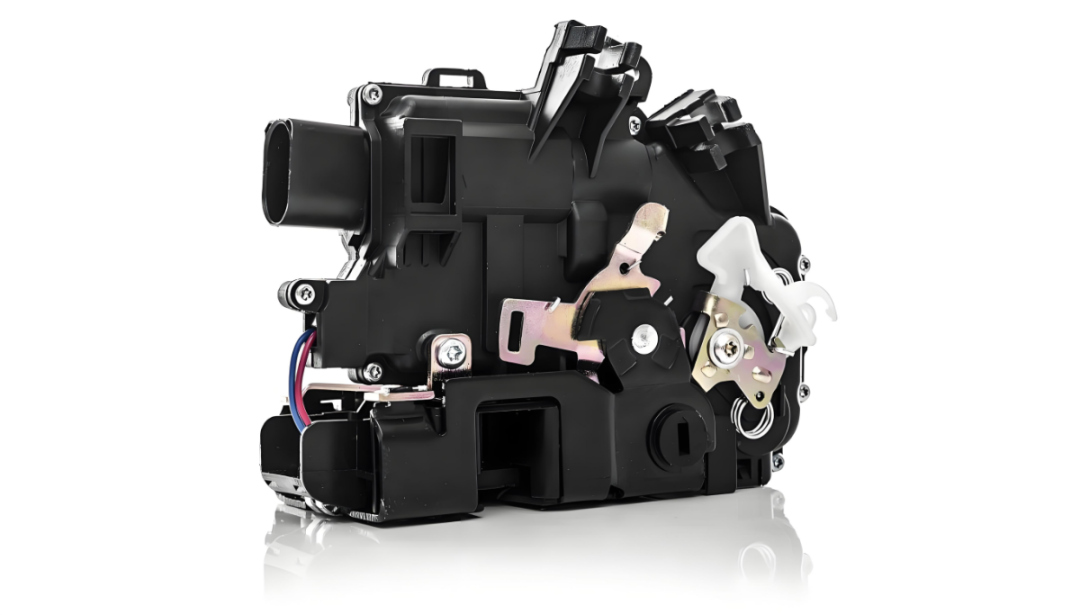
To enhance the consistency of door lock products and production efficiency, more and more car manufacturers are introducing automated production lines into their assembly processes. However, due to the varying workstation conditions and component shapes, new challenges arise. Danikor has delved into the field of car door lock assemblies, aligning with customer perspectives and challenges, to provide a variety of reliable automated assembly solutions and services.
1. Synchronous Tightening in Vertical and Horizontal Directions
For the same door lock component at the same workstation, it is often necessary to perform synchronous tightening operations in both vertical and horizontal directions to maximize the use of workstation space and improve the overall production line cycle time.
Solution: For the same product workstation with the same screw specifications, when there is interference at the tightening position or the fixture affects the operation, a vacuum suction module is used. The length of the suction tube can be chosen based on the required avoidance distance. Additionally, a single screw feeder can be paired with two sets of modules to simultaneously supply screws to two tightening positions, effectively saving equipment costs.
For tightening positions without interference, a blow-and-tighten module can be directly used. This method has a simple action logic and further enhances the screw feeding cycle.
2. Self-Tapping Screws in Plastic Components
During the tightening process of self-tapping screws in plastic components of car door locks, issues such as stripped threads and over-tightening can occur, leading to tightening failures and affecting product quality and production line cycle time.
Solution: Using intelligent tightening tools, the corresponding process torque and tightening strategies can be pre-set. These tools not only have a fast tightening cycle but also maintain stable performance during high-volume tightening. Additionally, they can monitor the torque or angle at each step of the tightening process, promptly detecting tightening abnormalities such as floating locks and stripped threads, thereby improving the quality and consistency of tightening.
3. Automated Feeding of Components
In addition to screw assembly requirements, the assembly process of car door locks also involves the need for automated feeding of some components. Due to significant differences in appearance and shape, especially when two types of irregular materials need to be fed simultaneously, the traditional manual feeding method is inefficient and prone to errors.
Solution: A flexible vibratory feeder combined with camera recognition and robot picking is used. For irregularly shaped plastic and metal components, custom trays can be designed to increase the probability of the correct orientation of the materials, facilitating camera recognition and robot picking.
.gif)
For the simultaneous feeding of two types of irregular materials, a single robot can be paired with two vibratory feeders. By using vibration isolation fixtures, the mutual vibration effects on material orientation and the robot's high-speed movement can be avoided.